With the education and best practices we have learned, we are no longer fire-fighting and are much more proactive in meeting our customer’s needs.
Plant Production Manager
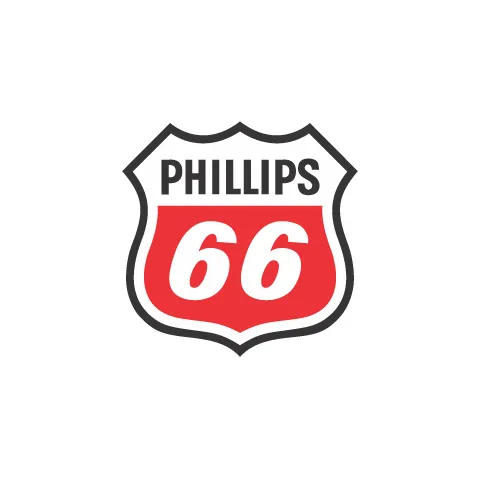
Fortune 100 Refinery & Lubricants Manufacturer
A Fortune 100 diversified energy manufacturing and logistics company with a portfolio of businesses: Midstream, Chemicals, Refining, and Specialties including lubricants. Pioneering leaders and ground-breaking product lines have helped them evolve into the fourth-largest finished lubricants supplier in the United States. Reaching across every key lubricant market, including automotive, trucking, agriculture, aviation, power generation, mining, and construction.
CHALLENGES
- Rising raw materials, packaging and finished goods inventory
- Inconsistent customer service levels
- Excessive fire-fighting and order expediting
- No supply chain integration across their processes, key functions and geographies
- Supply and production strategies not aligned with master data
- Very low SAP utilization and knowledge of system best practices
- Planning outside of SAP in multiple disconnected tools
- Frustrated users and excessive manual work being done
- Lack of trust in the system leading to ineffective use of MRP generated production planned orders and purchasing requisitions
- Multiple points of promise and unclear escalation and prioritization processes
- SAP reporting functionality not being utilized to support business and process performance KPI’s
SOLUTIONS
- Supply Chain transformation utilizing Reveal’s oVo® methodology focused on improving service levels, optimizing inventory, capacity and production planning and data visibility
- Established Supply Chain end-to-end planning inside of SAP, integrating core processes across the organization
- Education for buyers, planners, schedulers, shop floor and management on existing SAP tools
- Education, ownership and accountability of master data and aligning MRP strategies
- One-on-one sessions with management and executives to drive management decisions using SAP
- Set KPI’s aligned with strategic business performance objectives
BENEFITS
- $15 MM reduction in average inventory
- 98% reduction in overdue supply and demand elements
- 86% reduction in negative days of supply
- Reduced SAP exception messages by 73%
- An integrated business utilizing one system of record – SAP
- Increased data accuracy, process efficiencies and user confidence leading to better decision making
- Improved capacity and material availability accuracy
- Demand-driven planning via MRP requirements
- Increased analytics capability and visibility across the supply chain
- Educated and empowered users and management team
- Aligned KPI’s to business objectives
- Ability to migrate to S/4 HANA