We have to use the oVo ® Methodology, it ’s proven, we are believers at this point, we are evangelicals about the Reveal Methodology!
Tim Baker
Sr. Vice President IT
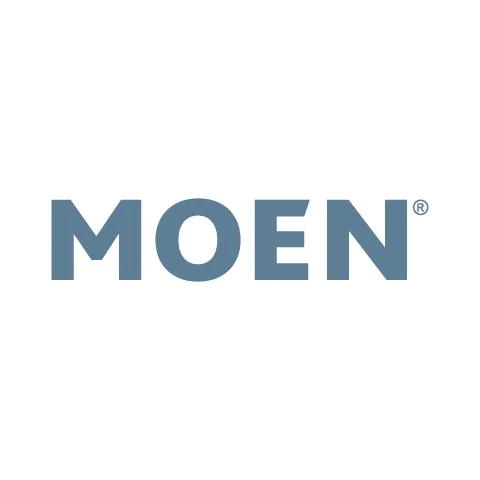
Moen is one of the world’s largest manufacturers of plumbing supplies, including kitchen and bath faucets, shower heads, accessories, bath safety products, garbage disposals and kitchen sinks for residential and commercial applications. The organization has plants both in North America and China running on SAP ECC.
CHALLENGES
- Limited ability to produce a dependable Available to Promise date negatively effecting Moen’s ability to increase service levels
- Excessive working capital tied up in inventory
- Limited understanding of SAP and its functionality and analytic capability
- Unclear and differing business processes across the plants and organization
- Component constrained production schedules
- Constant “outside of the system” practices to procure materials and schedule production orders
- A lack of planning inside existing and standard SAP functionality
- Lack of trust in the system leading to ineffective use of MRP generated production, planned orders and purchase requisitions
- Unable to measure the actual costs of a production run and margins
- Difficult to measure plan and schedule attainment
SOLUTIONS
- Supply Chain transformation utilizing Reveal’s oVo® methodology focused on improving service levels, optimizing inventory, capacity and production planning and data visibility
- Education for buyers, planners, schedules, shop floor and management on existing SAP tools
- Education, ownership, and accountability of master data and aligning MRP strategies
- Implemented Discrete manufacturing methodologies for scheduling, capacity and production planning in SAP
- Introduced multi-level costing to enable measures of costs and margins at a production order level
- Set KPI’s and aligning with strategic business performance measures
BENEFITS
The combination of the conversion to Discrete with the oVo transformation:
- Schedule attainment for the aggregate Sanford Plant rose from 59% to 93%
- Reduced inventory while improving customer service levels
-25% reduction in WIP
-Total inventory reduction by 15%
-Processes improved and standardized resulting in a reduction in planning and scheduling time - Year over year cycle count adjustment improvements of 55% Reduced Scrap
- Improved capacity and component constrained schedule to Production