Working with the Reveal team was one of the best consulting experiences in my career from both a people and business outcome perspective.
VP of Operations & CI
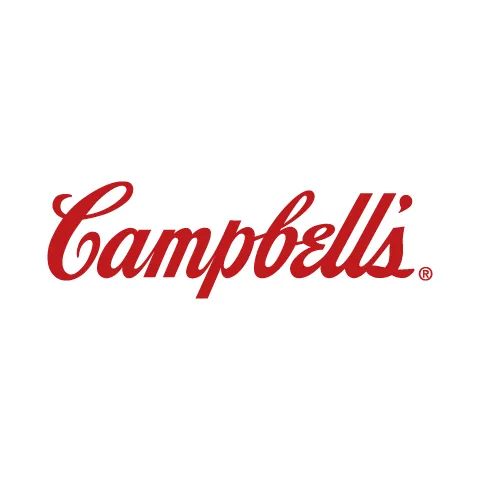
Campbell’s Soup is a manufacturer of food products including soups, sauces, and beverages. These products are sold to retail grocers and food service companies. The soup division operates 4 North America manufacturing locations and the company implemented SAP ECC with the following business objectives: improved customer service levels, optimize inventory levels, improve production schedule attainment, improve operational effectiveness and reducing operating costs.
CHALLENGES
- Rising raw materials and finished goods inventory
- MRP and its support of purchasing automation not understood
- Inventory strategies and master data not aligned
- Excessive order expediting
- Frustrated users and excessive manual processes
- Customer service levels were maintained with excessive amounts of inventory
- Lack of trust in the system leading to ineffective use of MRP generated production planned orders and purchasing requisitions
- SAP reporting functionality not being utilized to support business and process performance KPI’s
- New corporate materials management group created in 2016 with no common materials management process
SOLUTIONS
- Focused on improving service levels, optimizing inventory, capacity and production planning and data visibility
- Established ownership and accountability of master data and aligning MRP strategies
- Focus on key materials using standard SAP tools to achieve the highest value return in the shortest possible time
- One-on-one sessions with management and executives to drive management decisions using SAP
- Education for buyers, planners, schedulers, shop floor and management on existing SAP tools
- Education on managing master data to manage the business
- Established Process Aligned Teams (PATs) to address daily supply chain challenges identified through the oVo® process
- Supply Chain transformation utilizing Reveal’s oVo® methodology
- Set KPI’s and aligning with strategic business performance measures
BENEFITS
- Saved $40 million in one year on SCM operations and $53 million since start of project
- Inventory reduction of over 39%
- Inventory turns improvement of 38%
- Optimized 100% of average value of inventory
- Improved capacity and material availability accuracy
- Improved schedule attainment
- Improvement in Operational Service Levels
- Reduced Red Lights (overdue supply chain elements) by 98%
- Reduced Exception Messages by 95%
- Simplification and standardization of procurement processes
- Educated and empowered users and management team
- Aligned KPI’s to business objectives