The Daily Grind: A Common Supply Chain Scenario
Have you ever had a day, week, or start of a supply chain action that made you feel that you are either staring up a cliff with no idea of where and how to start the ascent or at the edge of an abyss and afraid to step forward for fear of plunging into the unknown? In the meantime, the phone is ringing off the hook, emails are backing up, and your boss has summoned you to a crisis meeting…
Anyone who has worked in a supply chain setting, be it as a purchaser, planner, functional specialist, or department manager, will understand what it is like to have an unhappy customer, agitated shop floor, or disgruntled boss demanding answers and immediate action. Satisfying others might not be an easy task, though, if cash is tight, business is uncertain, and sales orders are not being placed as expected. Would it not be so much better to delay or even cancel purchase orders? By doing so, you could potentially avoid a firefight action to reduce inventory instead of a fire-sale approach that burns cash.
Imagine if you had information in hand that would give you a heads-up that something might be awry, that there is a risk of service degradation on the horizon, or that you may be receiving inventories likely to be in excess of demand. Now, magnify these situations by thousands of materials or stock-keeping units. How on earth does someone wrap their arms around all these materials to proactively manage the supply chain, be they components or finished goods? And how can they possibly avoid the crisis interventions and potential over or inadequate action.
“Management by Exception” is a system of spotting and responding to a situation only in those cases where there is a requirement to take action. In the most efficient and best possible manner, the end goal is to resolve a deviation from the routine or expected business results.
As a result, there is more available time to apply critical thinking and experience to resolving significant variances that could result in service issues in the supply chain. In addition, it becomes possible to detect and clear the hurdles which need decision-making and take the best suitable actions. Using Management by Exception, supply chain operations is provided with a concise, unvaried detailed status report covering all aspects of the issue.
Three Pillars of Exception-Based Management: A Critical Analysis
To truly become exception-minded in your approach, there are three critical aspects of understanding required. Without these, an exception-minded approach will evade you in the wash of false signals, contradictions, and red herrings.
1. First Principles
- A supply chain is focused on time and quantity, i.e., how much of an item is needed and when?
- A Materials Requirements Plan (MRP) assumes infinite capacity, i.e., there is demand in units at a point in time and we will plan to fill it.
- SAP is demand-driven; exceptions and warnings are based on the supply plan and the inability thereof to satisfy the demand.
2. Master Data
MRP will use master data or business rules to plan the supply in response to demand. So it is essential on the MRP1 through MRP4 views of a material master to reflect the reality of the business environment. Not doing so will generate and re-generate exception messages, propose supply plans that are not feasible, and lead to inefficient business processes and the risk of service degradation.
3. Housekeeping
MRP will always assume open MRP elements as valid and will use these elements in the planning process. For example, MRP believes that the purchase order with a quantity of two units and a delivery date of four years ago has an imminent arrival or that the sales order with a delivery past due for last.
{{reveal-tv-promo}}
Set the Expectation: Keep Calm, Use SAP
SAP has an impressive setup providing several features to support exception monitoring and prioritizing action to balance demand with supply. Yet often, these features are rarely used to their full potential and/or are misunderstood.
The most noteworthy difference is between the Stock Requirements List (t-code MD07/MD04) and the MRP List (t-code MD06/MD05). The Stock Requirements is akin to a material ledger, i.e., it is a complete list of all materials whether a planning relevant change has been made or not. When used in conjunction with the From Date, the MRP List lists materials that have had a planning change because of the MRP functionality being executed.
This is an important distinction, as it indicates what we call the "now business", representing a planning change to have supply meet demand. Why look at materials that have not been impacted by planning and have not received an MRP relevant change since the last time you looked at it? It is not that we prioritize one over the other; it is just that the focus and usability of the data contained in the reports are different. We would strongly argue that both perspectives are essential.
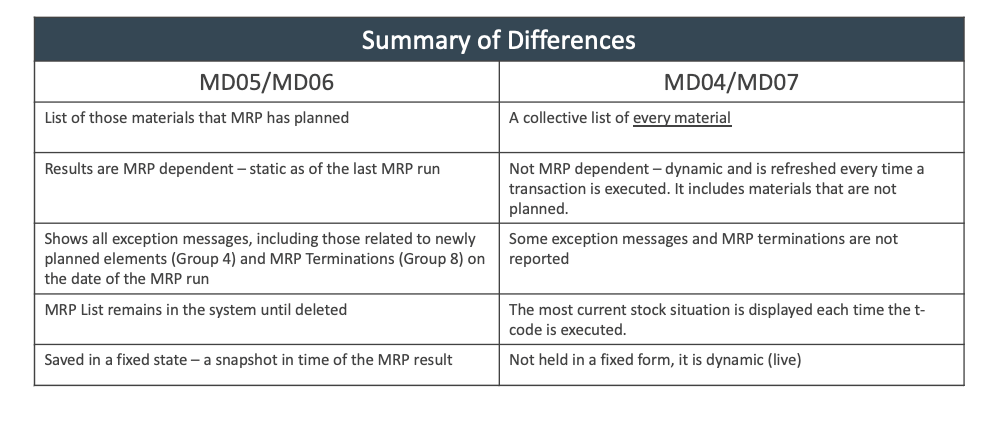
Housekeeping, i.e., making sure MRP elements or transactional elements (Sales Orders, Purchase Orders, Goods Receipts, etc.), must reflect current and actual reality. MRP will regard open elements as valid for planning purposes, even if years in the past.
Here is an example of the most fundamental impact that can cause disruption. A new sales order comes in for delivery seven days from now, and we do not have an inventory position. We have an open purchase order with an available quantity for delivery that is two years ago. MRP will generate an exception to schedule/expedite the delivery but will not generate a new purchase requisition.
MD07 is especially useful since it is the most reliable source of all elements that may impact future MRP lists when the next MRP is executed. Using MD06 for Housekeeping limits the selection to materials that were only affected by the last planning run. Future exception messages can be generated by outdated elements the next time a plan is proposed. It is far better, then, to proactively manage MRP Elements, ensuring materials dates and quantities reflect the reality.
The number of exception groups and messages is too broad to elaborate on in just one discussion. What is clear, however, is that with clean data, daily process, and discipline, an exception-minded approach is achievable and provides focus to balance and optimize the supply chain, set priorities, and improve service levels.
More Expert Insights & Exclusive SAP Secrets
For in-depth insights and SAP video education, visit Reveal TV to explore this topic further or sign up for exclusive content.